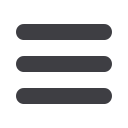
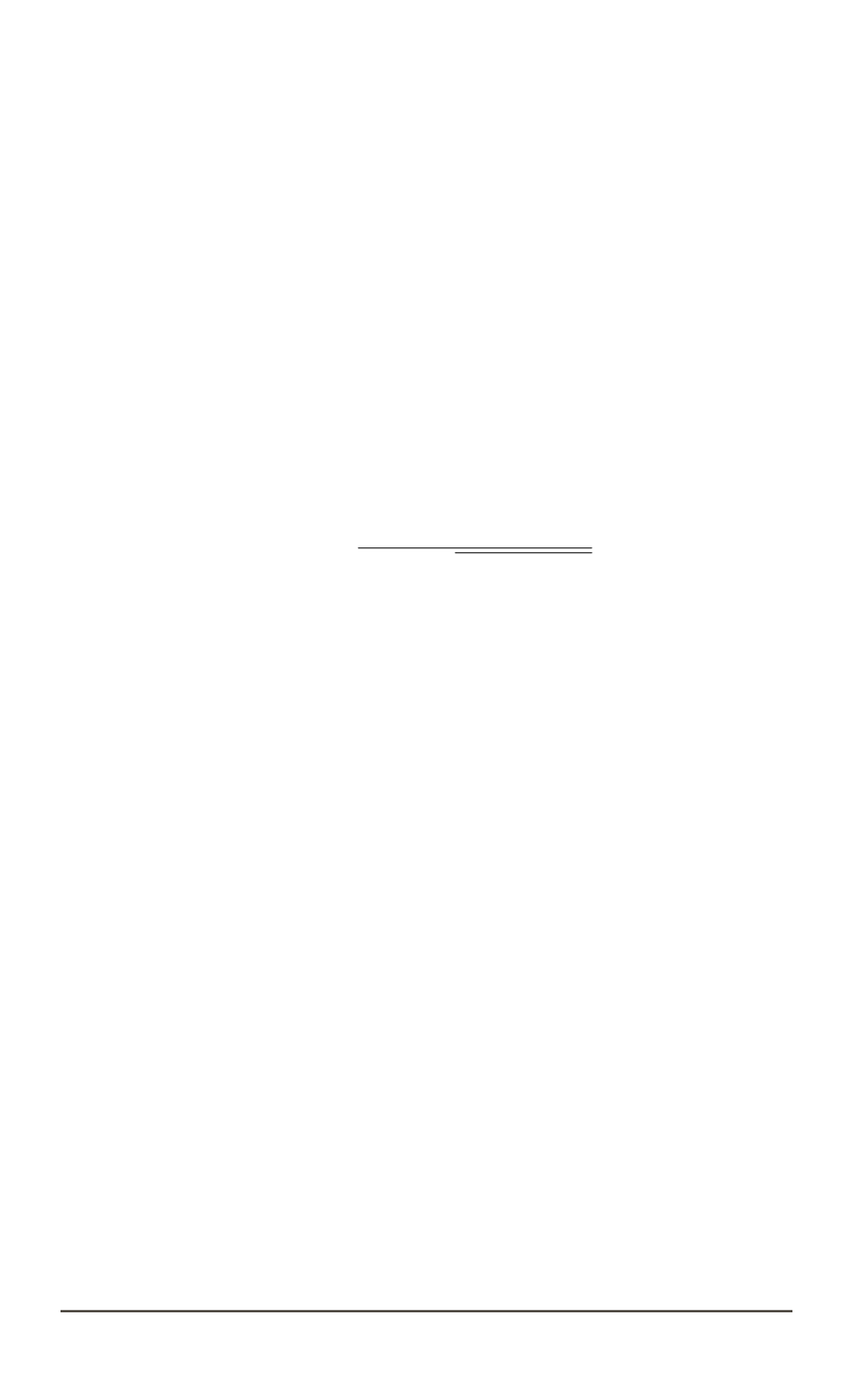
the “joined” points. The points on the boundary occupied by the medium
(Euler cells containing these points have at least one empty cell among their
adjacent cells) are excluded from this rule. If one Euler cell contains several
individual points, one of which is a boundary point, only the boundary
point is used for calculation and all the other points are excluded from the
calculation.
After redistribution of the individual points among the cells of the Euler
mesh the described computational procedure is repeated. An artificial
viscosity [1] is introduced into the described computational scheme
for continuous calculation of the shock waves. In case of the medium
compression this viscosity gives a summand added to the hydrodynamic
pressure acting at this point (a combination of linear and quadratic artificial
viscosity is used).
Integration time step
Δ
t
is selected under the Current stability condi-
tion [1] and it meets the following inequation:
Δ
t <
min
(
i,j
)
Δ
l
c
(
i,j
)
+
q
v
2
r
(
i,j
)
+ v
2
z
(
i,j
)
,
here
c
(
i,j
)
is speed of sound at Lagrangian points,
Δ
l
is least of the Euler
mesh steps along the radial (
Δ
r
) and axial (
Δ
z
) coordinates (generally, the
Euler mesh with square cells is used where
Δ
r
= Δ
z
).
The described above computational algorithm is implemented in the
numerical simulation software ERUDIT (Russian abbreviation for Heuristic
Calculation of Ordered Motion of Individual Points) developed at Bauman
Moscow State Technical University which was used in the presented
research. Computational method described here was tested while solving a
wide variety of explosive and impact continuous medium loading problems
(as well as penetration problems) and showed positive results [10–12]. One
of its advantages is the ability to calculate a motion of the continuous
medium with large deformations without using specialized procedures of
computational mesh regeneration.
In order to penetrate into the targets made of high-strength steel
of a large width (more than 500 mm) elongated metal projectiles are
used which have speed of approximately 1500 m/s. As it was mentioned
above such projectiles penetrate into the targets in a hydrodynamic mode
(when the projectile material spreads around the target contact area with
the corresponding reduction of the projectile length during penetration).
According to the hydrodynamic theory of penetration [2] the main factors
affecting the target cavity depth are the following: a projectile length and its
material density. Elongated projectiles made of the high density materials
must be used for increasing a penetration depth. Such materials include
70 ISSN 0236-3941. HERALD of the BMSTU Series “Mechanical Engineering”. 2015. No. 1