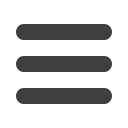
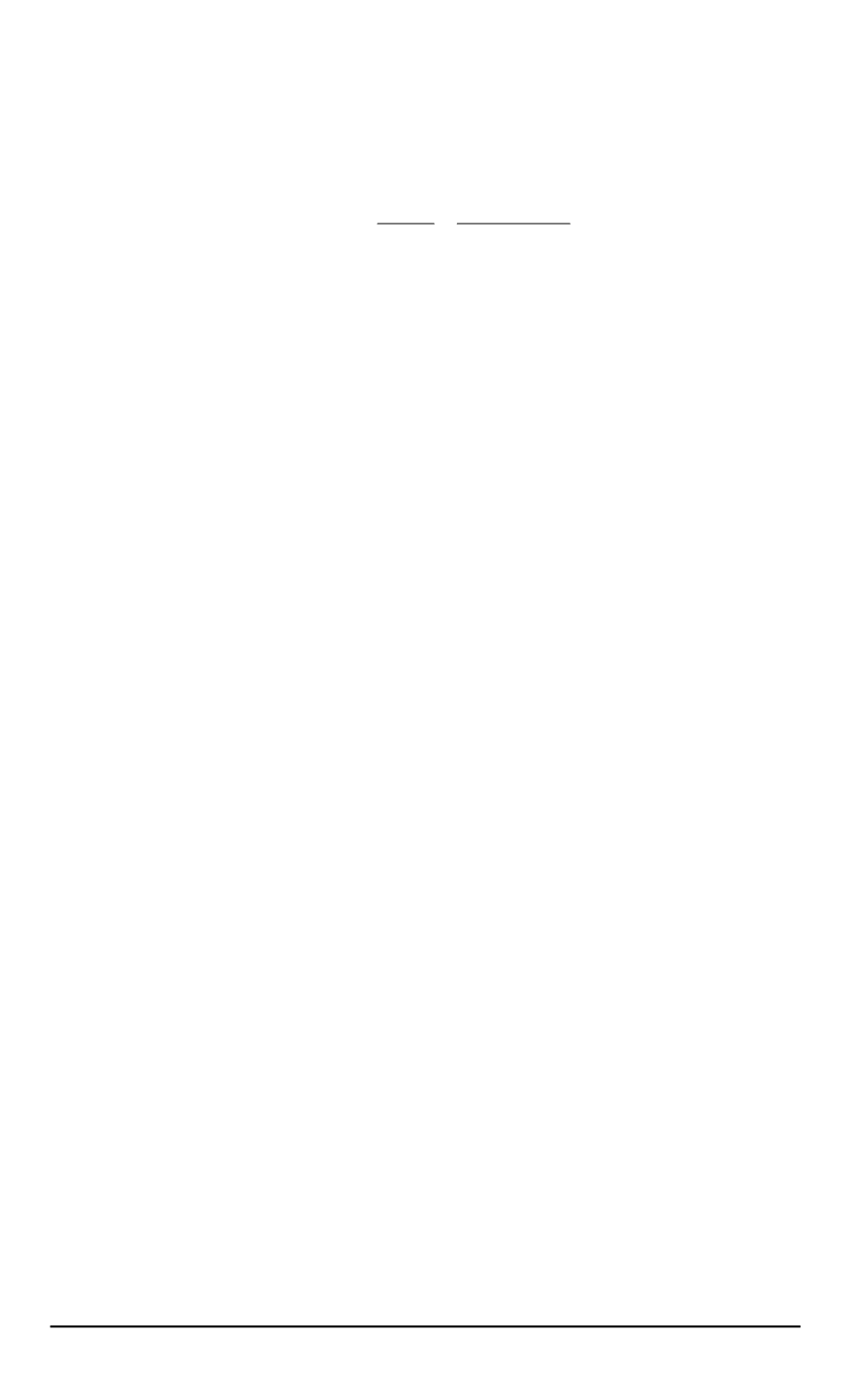
the flow pattern changing as well (Fig. 4
b
). Experimental angle of the
shockwave front deflection from the wedge (
α
= 13
◦
,
β
= 5
◦
for the
lower 10
◦
wedge) was used to calculate the Mach number for the ram air
according to the formula [5]
M
= sin
2
α
−
γ
−
1
2
∙
sin
α
sin
β
cos(
α
−
β
)
−
1
/
2
.
Mach number for the lower 10
◦
wedge was 7.09 (Fig. 4
a
). The flow
parameter values for a semi wedge can be estimated with lesser accuracy
(a greater angle of shockwave deflection from its upper surface can be
observed), which is caused by the model being at a distance from the
nozzle symmetry axis.
Under similar initial conditions flow tests were conducted on models
simulating air intake of a pespective HA. These models were represented
by two blunt-nose 10
◦
wedges with 1.5 mm bluntness radius and 10 mm
thickness. In order to investigate shockwave interaction in a complex
configuration duct simulating flame holders in the gas dynamic passage,
the models were provided with special cavities, 3 mm deep. The models
were positioned symmetrically to the nozzle axis at 2 cm distance from
each other. This was done to ensure homogeneous field flow parameters
between the models. Fig. 5 presents shadow images of the test.
The process presented in Fig. 5,
a
is caused by the first stage of the
driven gas expansion through the nozzle on to the model, which is optimally
suited for the high-speed test, since at this period the flow parameters from
the nozzle unit are approximately constant, with M
= 7
. At the shadow
video it is experimentally observed for 15 ms.
After the rarefaction waves fan and the contact surface of the driver gas
hit the LPC right end wall, the pressure at the nozzle entrance decreases
and the flow parameters start to fluctuate significantly. This perturbation
is shown in Fig. 5
b
, it lasts for about 5. . . 7 ms. After that the shockwave
interaction process in the shock tube is determined by multiple passes and
rarefactions of shock waves between LPC and HPC sidewalls. However,
it is possible to identify time intervals in which gas parameters at the
nozzle entrance change insignificantly. Such type periods can be directly
connected and numerically characterized with the data presented in the
oscillograph pattern (Fig. 3
c
). In particular, fragment
C
in the oscillograph
pattern corresponds to the second, lower velocity quazi steady flow mode
presented in 5 c. The duration of this period is
t
c
≈
30
ms, M
= 4
.
5
.
In the course of the experiments the third quazi steady flow stage
( M
∼
= 3
) was identified which corresponded to fragment
D
of the
oscillograph pattern in Fig. 3.
ISSN 0236-3941. HERALD of the BMSTU. Series “Mechanical Engineering”. 2015. No. 1 9