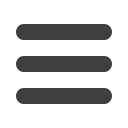
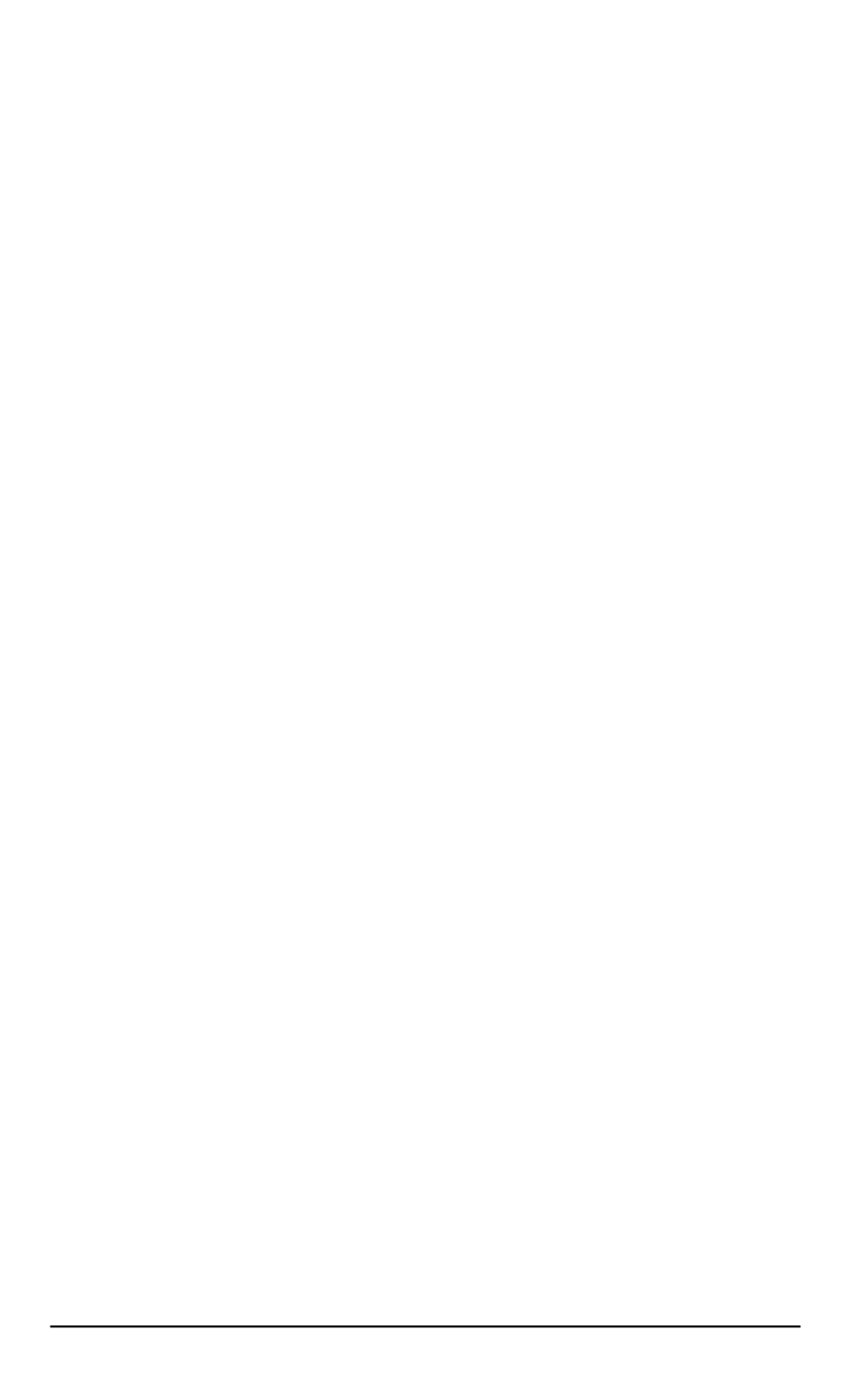
•
different-thickness sharp wedges;
•
same-thickness sharp wedges with internal trapezoid cavities;
•
same-thickness blunt nose wedges with internal trapezoid cavities.
There exist various classifications [5, 6] of gas dynamic experimental
setups ranging from transonic to hypersonic velocities. Since research in
this field covers fundamental investigation of HA aerodynamic performance
(including hypersonic ramjet propulsion unit), particular attention should
be paid to the measurement accuracy issues in short duration aerodynamic
tests [6]. The research in question used the hypersonic shock tube at the
Institute of Problems in Mechanics of RAS [7–10] which operates on the
impulse-type wind tunnel principle and enables supersonic and hypersonic
flow investigation for the aircraft mockups and their individual structural
elements [1].
Consideration of hypersonic patterns interaction in various duct configu-
rations is preceded by the analysis of the test data on shockwave flow
pattern in the shock tube. It is demonstrated that the multiple passage of
the shock waves through the shock tube enabled creation of several quasi
steady hypersonic flow modes.
The shockwave interaction pattern for the models tested was reproduced
in numerical experiments using proprietary computer code.
Experimental setup description
. The hypersonic shock tube was
designed for the experimental investigation of aerodynamic flow field
structure around scaled models at supersonic and hypersonic velocities
[7–10]. The overall length of the installation is 14.5. . . 22 m, which can be
varied depending on the desired flow parameters. It comprises three to five
segments. High pressure chamber (HPC) is made out of corrosion-resistant
steel, is 1.97 m in length and 8 cm in cross section diameter. This segment
operates with room temperature gases at the pressure up to 22 bar. Low
pressure chamber (LPC) is 7.35 in length and has the same cross section
diameter. LPC is made out of corrosion-resistant steel and is separated
from the HPC by a membrane. These segments can be elongated by 7.5 m
with extra segments.
A nozzle unit is installed at the end of the LPC with an aluminium
diaphragm at its entrance. This diaphragm is ruptured by the initial
shockwave, thus the flow expands through the nozzle into the receiver.
The models tested are placed in the receiver and can be positioned at the
nozzle exit or at some distance from it.
The hypersonic shock tube is equipped with piezo electric sensors to
record shockwave interaction in the course of the experiment. The setup is
shown schematically in Fig. 1. One sensor (
A
) is placed at the beginning of
the HPC and is used to identify the compression/rare faction waves hitting
the section wall. The other sensors (
B
,
C
) are positioned in the middle and
ISSN 0236-3941. HERALD of the BMSTU. Series “Mechanical Engineering”. 2015. No. 1 5