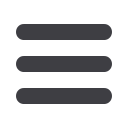
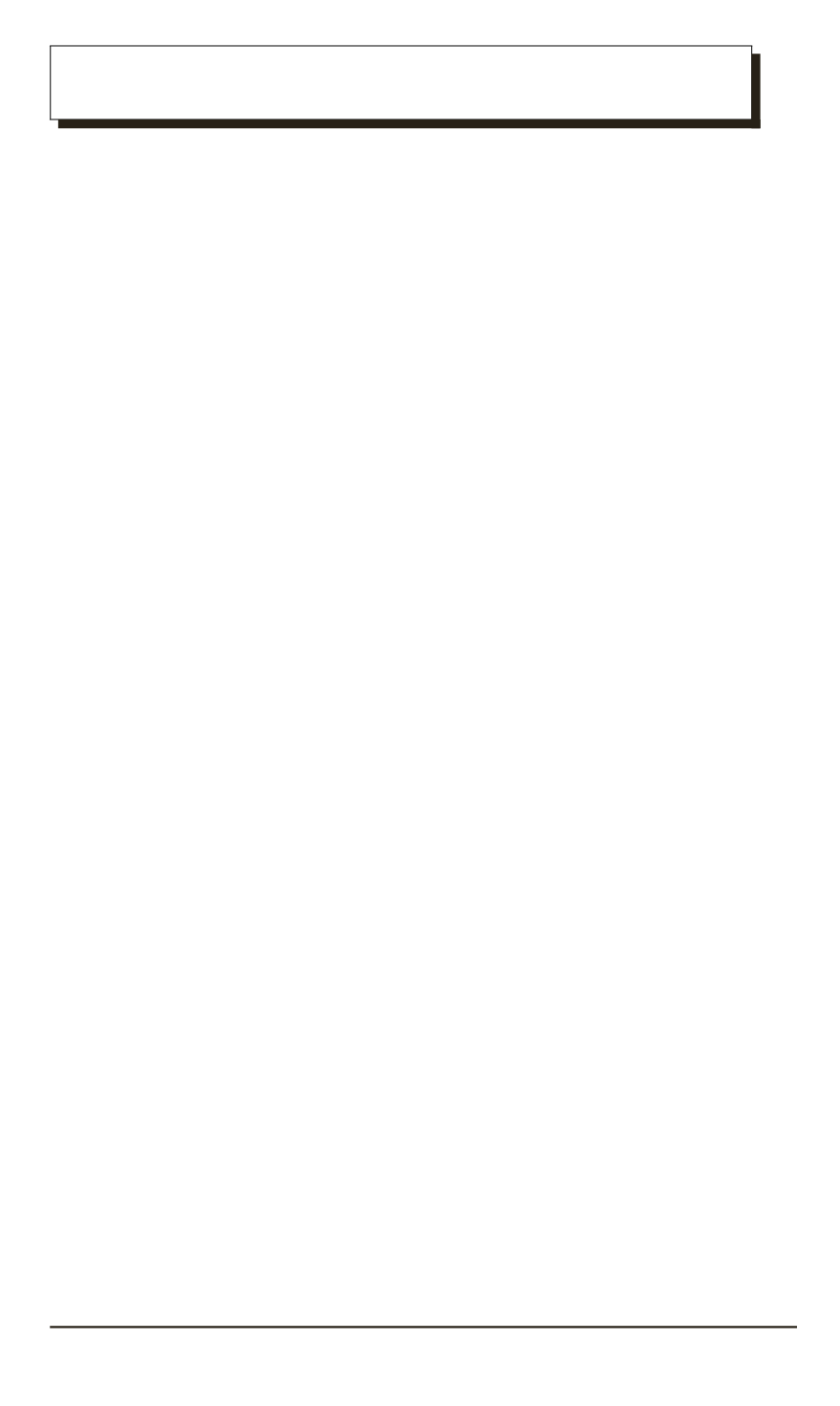
THERMAL, ELECTRIC JET ENGINES
AND POWER PLANTS OF AIRCRAFTS
THERMAL HYDRAULIC EFFICIENCY OF COPLANAR COOLING
CHANNELS FOR LIQUID ROCKET ENGINE CHAMBERS
V.P. Alexandrenkov
Bauman Moscow State Technical University, Moscow, Russian Federation
e-mail:
aleks@power.bmstu.ruThe paper considers the coplanar circuits (with cross finning) used for cooling
liquid rocket engines by means of the maximal heat removal criterion. The available
experimental data on the convective component of heat loss are used to perform
computational and analytical analysis of the influence of both thermal hydraulic flow
characteristics and finning parameters on their efficiency. The possibility of using the
proposed methodology for evaluating the heat transfer efficiency in the conventional
finned circuits with regard to the coplanar flow peculiarities is demonstrated. The
domains of finning parameters are defined with a significantly higher (2–4 times)
efficiency in comparison with the conventional finning of the cooling channels.
Keywords
:
circular coplanar channel, cross-finning, convective heat transfer
intensification, efficiency, maximal heat removal, finning parameters, thermal
hydraulic characteristics.
Cooling channels of liquid rocket engines (LRE) chambers are circular
channels formed by two shells joined with finning. As demonstrated in
[1] the finning factor significantly affects the efficiency of the firewall
cooling. It was also found out that under certain conditions the finning
factor can lead to negative results, i.e. lower heat removal as compared to
the reference smooth channel without heat transfer intensification (HTI).
Therefore, the heat transfer intensification of the convective component is a
critical problem in terms of an additional or countervailing measure, which
can considerably increase the heat removal from the firewall in order to
achieve the required cooling conditions.
Taking into account the finning scale and technological constraints, the
well-known conventional methods of HTI such as “artificial roughness”
are quite limited in use.
The method of heat and mass transfer intensification in the circular
finned channels, so called the vortex or coplanar method, is described
and analyzed in [2, 3]. A coplanar channel (CC) (Fig. 1) is an innovative
structure of joined shells and cross fins on the opposite surfaces of the
circular channel enabling the cross flow of a heat transfer agent.
This design solution is a special type of the classic finned channel with
additional geometric parameters and the obvious specific nature of both
heat and mass transfer mechanisms and their calculation.
The model of physical flow in such a channel is a combination of
individual coplanar vortex flows formed by cross finning due to viscous
44
ISSN 0236-3941. HERALD of the BMSTU. Series Mechanical Engineering. 2015. No. 2