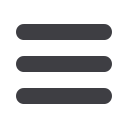
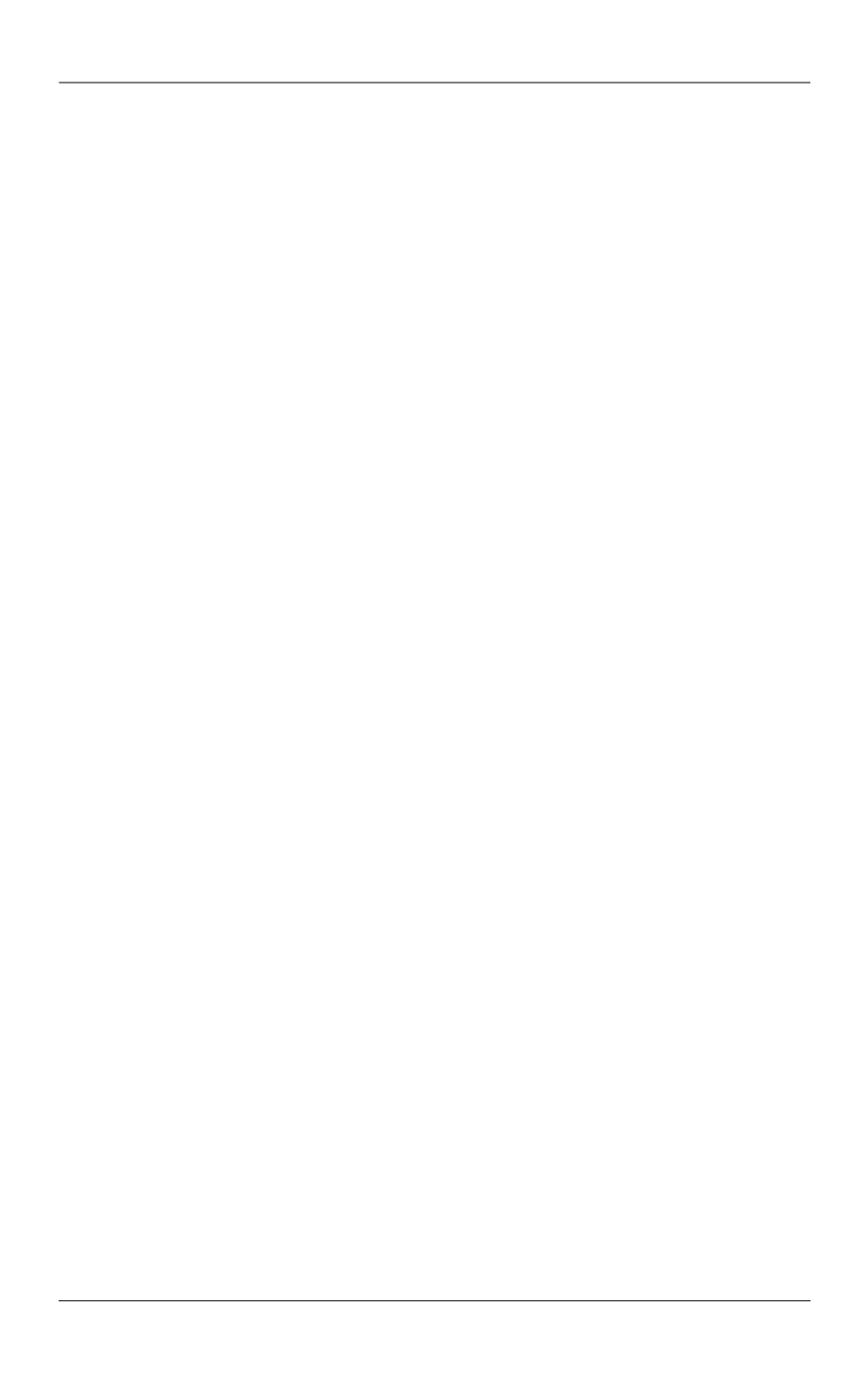
A. Eremichev
26
ISSN 0236-3941. Вестник МГТУ им. Н.Э. Баумана. Сер. Машиностроение. 2017. № 5
a
= 38,0 mm,
b
= 8,0 mm,
c
= 10,0 mm,
r
= 4,0 mm
and the second
a
= 38,0 mm,
b
= 6,0 mm,
c =
6,3 mm,
r
= 3,0 mm.
Samples of the first series were almost the same as tested earlier plexiglas samples.
For CCCM the depth and width of the groove led to the destruction of the sample not
at the working area, and to the "puckering" of the carbon fibers of those parts of the
sample, which is attached to the gripper of device. It is associated with a significantly
lower binding strength compared with the strength of carbon fiber. The destructive
stress in this case was very little of 0,507 MPa to 0,863 MPa.
The second series of samples from CCCM have reduced width and depth of grooves.
This has led to the growth of destructive stresses almost 20 fold. However, in this case, the
destruction of the samples occurred not in the working area. Observed cracking close to
one of the grips of the device. Stresses in the working area of the sample at this point was
approximately 25 % of the tensile strength CCCM under uniaxial tension.
Thus, the task to determine the strength under three axial tension CCCM at this
stage of the work failed. In our opinion it is necessary to increase the size of samples
a
and a relative decrease in the depth
c
and width
b
of groove. It is connected with great
difficulties due to the high value of the samples CCCM and the limited capacity of the
test equipment.
Conclusion.
The device and the sample, which can be successfully applied to
study the properties of materials under three axial tensile were developed.
The proposed method of test for three axial tension can be successfully applied to
orthotropic materials such as plexiglass.
The use of the above described methods for investigation of materials like CCCM
requires further development. It is necessary to increase the size
a
of samples and a
relative decrease in the depth
c
and width
b
of groove.
REFERENCES
[1] Wu H.-C. Continuum mechanics and plasticity. Chapman & Hall/CRC Press, 2005. 684 p.
[2] Feodos'ev V.I. Advanced stress and stability analysis. Berlin, Heidelberg, Springer-Verlag,
2005. 421 p.
[3] Doquet V., Ben Ali N., Constantinescu A., Boutillon X. Fracture of a borosilicate glass
under triaxial tension.
Mechanics of Materials
, 2013, vol. 57, рр. 15–29.
DOI: 10.1016/j.mechmat.2012.10.008
Available at:
http://www.sciencedirect.com/science/article/pii/S0167663612001810[4] Eremichev A.N. Ustroystvo dlya trekhosnogo nagruzheniya obraztsa nagruzkami odnogo
znaka [Test device for uniform triaxial tensile]. Patent USSR 1499170. Appl. 18.06.1987.
Publ. 07.08.1989.
[5] Eremichev A.N., et al. Obrazec dlya ispytanij na ravnomernoe trekhosnoe rastyazhenie
[The speciment for testing at uniform triaxial tension]. Patent USSR 1762165. Appl.
10.04.1990. Publ. 15.09.1992.