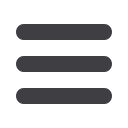
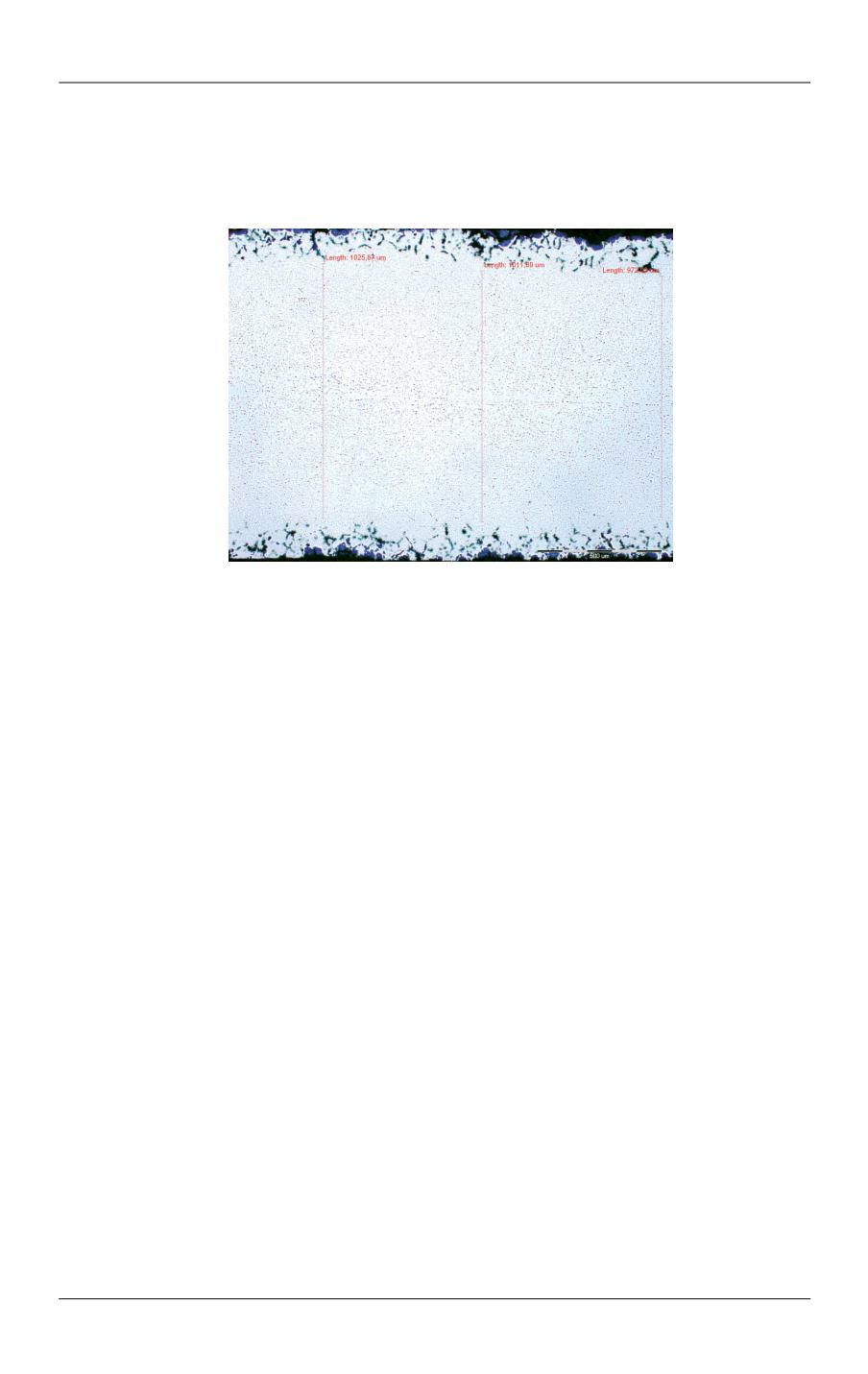
О.Ю. Козлова, С.В. Овсепян, А.С. Помельникова
38
ISSN 0236-3941. Вестник МГТУ им. Н.Э. Баумана. Сер. Машиностроение. 2016. № 6
Коррозионная повреждаемость азотированного материала при высокой
температуре была исследована на сплаве ВЖ171 по микроструктуре образца.
После выдержки 100 ч при 1200
о
С глубина поврежденного слоя на образце
толщиной 1,18 мм составила
105
мкм (рис. 5).
Рис. 5.
Глубина коррозионных повреждений азотированного сплава ВЖ171
после выдержки при 1200
о
С в течение 100 ч (×100)
Обсуждение результатов.
Установлено, что высокотемпературная ХТО по-
ложительно влияет на длительную прочность сплавов, содержащих титан
(ВЖ98, ВЖ171), значительно увеличивая время до разрушения при температуре
испытания 1000 °С. Это достигается вследствие образования стабильных нитри-
дов компактной формы. Нитриды титана крупнее, и их количество больше в
сплаве ВЖ171, чем в ВЖ98, из-за значительной разницы (почти в 4 раза) в со-
держании титана. Образующиеся в процессе азотирования игольчатые нитриды
на основе ниобия и алюминия в сплаве ВЖ159 охрупчивают материал, снижая
кратковременную и длительную прочность. Известно, что помимо снижения
характеристик прочности и пластичности, игольчатые нитриды приводят к об-
разованию пор в структуре материала [13].
Сплав ВЖ171, специально разработанный для азотирования, показывает
значительно более высокий уровень длительной прочности после ХТО. При
этом полученные значения относительного удлинения (9 % при 20
о
С и 25 % при
1000
о
С) соответствуют паспортным значениям на данный сплав [7].
Проведенные исследования влияния высокотемпературных процессов (от-
жига, азотирования и последующей выдержки в атмосфере) на микротвердость
показали, что образование дисперсных частиц упрочняющей нитридной фазы
способствует повышению в 2 раза микротвердости по сравнению с результата-
ми после отжига. Частицы нитридов по размеру отличаются в центре и по краю
образца, однако они распределены равномерно по всему сечению, что и под-
тверждают полученные значения микротвердости. После испытаний на жаро-
стойкость при температуре 1200
о
С на образце в местах коррозионных повре-